This morning I did another test run of the extruder, this time with the barrel temperature set to 110. I taped down a lot of things and installed a funnel so that the feed of polymer into the pump would require less attention.
Before I powered up I noticed that the auger bit was frozen from having its tip embedded in solidified polymer in the extruder barrel. I turned on the cartridge heater as usual but this time with the extruder barrel full instead of empty. After a few minutes thermal expansion of the melting polymer forced a bit of filament out of the extruder tip before the electric screwdriver was turned on. I tapped the on-button for the screwdriver and discovered that it rotated freely now.
At 110 Celsius the extrusion rate was considerably slower, but the filament tended to hold its shape better. The axial thrust on the auger bit seemed to be considerably stronger, too. The emerging filament still tends to foul on the extruder tip and thread as the length of the filament increases. Beveling the extruder tip like us done on the MK II design would be a great idea. I'll pursue that this weekend when I can get out the the drill press at my sister's house.
I took note of Adrian's experience with the filament swelling after leaving the extruder tip. The tip diameter to filament diameter proportion implied in Adrian's report was about 0.79. I worked backwards from this and determined that drilling a 3/32nds diameter hole in the extruder would result in a 3 mm filament. In practice that works out fairly close from the measurements I took this morning.
It seems obvious at this point that if we are going to extrude CAPA in this temperature range we are going to have to cool and support the filament almost immediately after it leaves the extruder tip. Otherwise it is going to draw into a thin thread because of the weight of the cooled filament end acting on the emerging polymer which, because it is molten, has a negligible tensile strength. Perhaps I can fabricate a little PTFE trough to provide that support.
08:45 PDT AKA 16:45 ZULU TIME 8 March...
It occurred to me that I had a little PTFE trough already made in the reject misdrilled bits of PTFE cylinder that I had made. I sawed one of those in half and taped it into place. You can see the result. (hmmm... pics don't seem to be uploading right now). The filament extruded into the trough all right but promptly adhered to the PTFE surface IN the trough. It seems that drilled PTFE surfaces are quite rough, a circumstance which probably explains how we can pump polymer through the PTFE thermal barrier in spite of the fact that the friction coefficient of PTFE is so low.
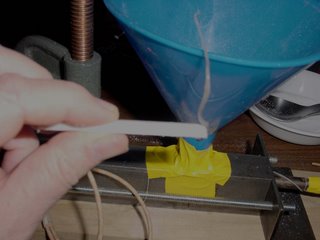
No comments:
Post a Comment